
UK-based engineering, procurement and construction (EPC) company Whittaker Engineering has developed a new water-backed welding procedure to reduce vessels’ dry docking periods.
The new technique uses high-powered induction heating coils to maintain a preheat temperature while welding water-backed plate, and to ease the heat loss through ships' hulls into the cold temperature of the sea.
Whittaker noted that induction heating requires huge currents rolling backwards and forwards through induction coils to generate high temperatures.
Cooling water and electricity flows through the coils from the power supply on deck and routed to the place where the welding is performed.
The power supply for the inductors has a maximum range of 75m from the power source on deck to the welding area.
EnQuest has already installed the new welding process on its Northern Producer floating production unit during routine work.
How well do you really know your competitors?
Access the most comprehensive Company Profiles on the market, powered by GlobalData. Save hours of research. Gain competitive edge.
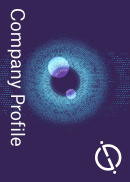
Thank you!
Your download email will arrive shortly
Not ready to buy yet? Download a free sample
We are confident about the unique quality of our Company Profiles. However, we want you to make the most beneficial decision for your business, so we offer a free sample that you can download by submitting the below form
By GlobalDataNorthern Producer operations manager Greig Ritchie said: “This is a truly noteworthy welding development that has helped EnQuest carry out work in the most efficient way.
“The procedure enables in situ modifications and repairs and avoids unnecessary and inefficient dry dock periods.
“It has significant potential for operators of vessels both in the North Sea and elsewhere.”
The new technology produces welding, which is ductile, low in hardness and of a high quality.
The technique, approved by Lloyd’s Register, can also be used to corrosion and pitting in the hull.
Whittaker Engineering founder Ken Whittaker said: “Many oil and gas vessels are expected to be at sea for 15 years or more. By carrying out the work offshore, we can potentially save companies millions of pounds by avoiding dry docking and loss of production through downtime.
“This is our fourth deployment and each one has been successful.
“Independent testing has also proved that our water-backed weld with induction heating is at least as strong and reliable as those carried out in a shipyard in the dry.”
The company designs, builds, supplies, fits, maintains and repairs components and equipment for the global marine and offshore industries.
Image: The new water-backed welding procedure to reduce vessels’ dry docking period. Photo: courtesy of Whittaker Engineering.