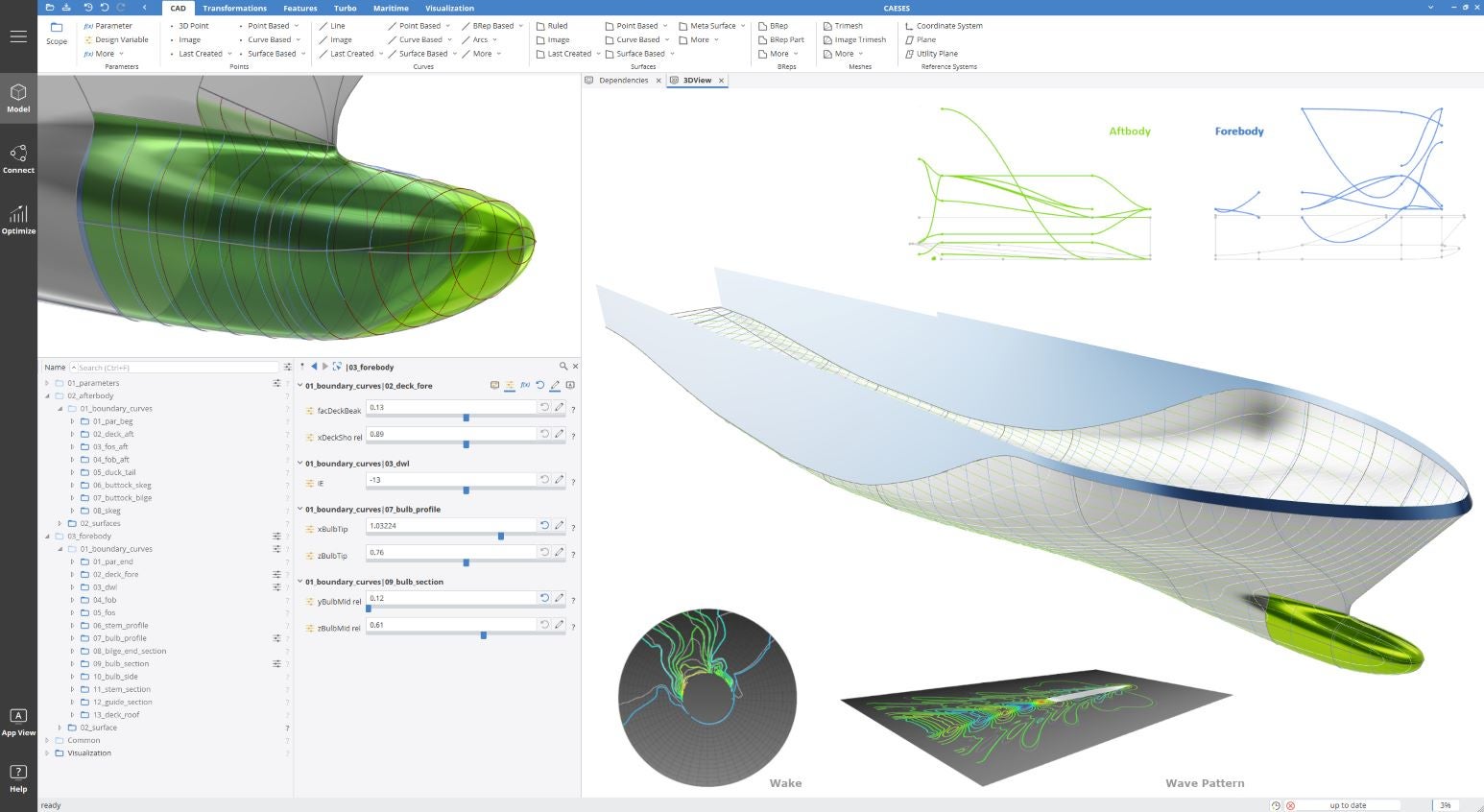
FRIENDSHIP SYSTEMS provides software solutions and services for the design and shape optimisation of ship hull forms, propellers and other components for marine systems, leveraging highly automated computational fluid dynamics (CFD) analysis.
Engineers increase the efficiency of their design process by automating and carrying out CFD-driven design studies using FRIENDSHIP SYSTEMS’ software solution, CAESES. This results in products with optimal fluid-dynamic performance and operational robustness.
Automated computer-aided design for optimal ship performance
CAESES is used worldwide by naval architects and marine engineers at leading shipyards and design offices to design highly efficient ship hull forms with reduced resistance and lower fuel consumption.
The company’s computer-aided design (CAD) and flow simulation process is completely automated so that no human interaction is required for design studies. This allows engineers to investigate large sets of designs in the shortest time.
FRIENDSHIP SYSTEMS collaborates with all major CFD vendors and open-source CFD packages.
Ship hull form design and shape optimisation with CFD
One of FRIENDSHIP SYSTEMS’ main capabilities includes full optimisation of ship hull forms using CFD and efficient geometry modelling techniques. The creation of different hull geometries and the corresponding CFD analysis is automated to run large studies on powerful workstations or HPC clusters.
The shape optimisation process can be based on innovative parametric models created from scratch in CAESES or on the modification of imported data from other design systems such as NAPA.
The CAESES platform offers integrated hydrostatic calculations and the option to carry out trim or speed studies. All types of hull form shapes can be developed, including container carriers, offshore supply vessels, tankers, yachts, and racing boats.
Propeller and thruster design for vessels
CAESES provides blade-modelling capabilities for the design of propeller blades and thruster systems, including hull-integrated thrusters such as the VOITH Linear Jet, as well as bow thrusters.
The shape of each blade can be customised using the CAESES platform, while the flow analysis is conducted automatically for each new design. As a result, thousands of propeller blade designs can easily be generated and assessed, developing a comprehensive design pool as a basis for design decisions.
Software for designing appendages and energy-saving devices on ship hulls
Furthermore, the CAESES platform allows engineers to design appendages and energy-saving devices to provide further fuel consumption savings for ship hulls. It helps engineers in finding the ideal shape and location of additional components to ensure the flow along the hull and propeller is optimised.
A variety of design configurations can be examined using the software, offering an advantage over manual engineering processes. This involves studying the shape and location pre-swirl and of propeller boss cap fins in addition to many other appendages.
Optimisation of vessel engine components
CAESES is also used to design highly efficient components for large marine diesel engines. This includes turbochargers where the turbine wheel, compressor impeller, and volutes are optimised.
Germany-based MTU Friedrichshafen uses CAESES for this purpose. Other applications include intake and exhaust manifolds, piston bowls, and fuel injectors.