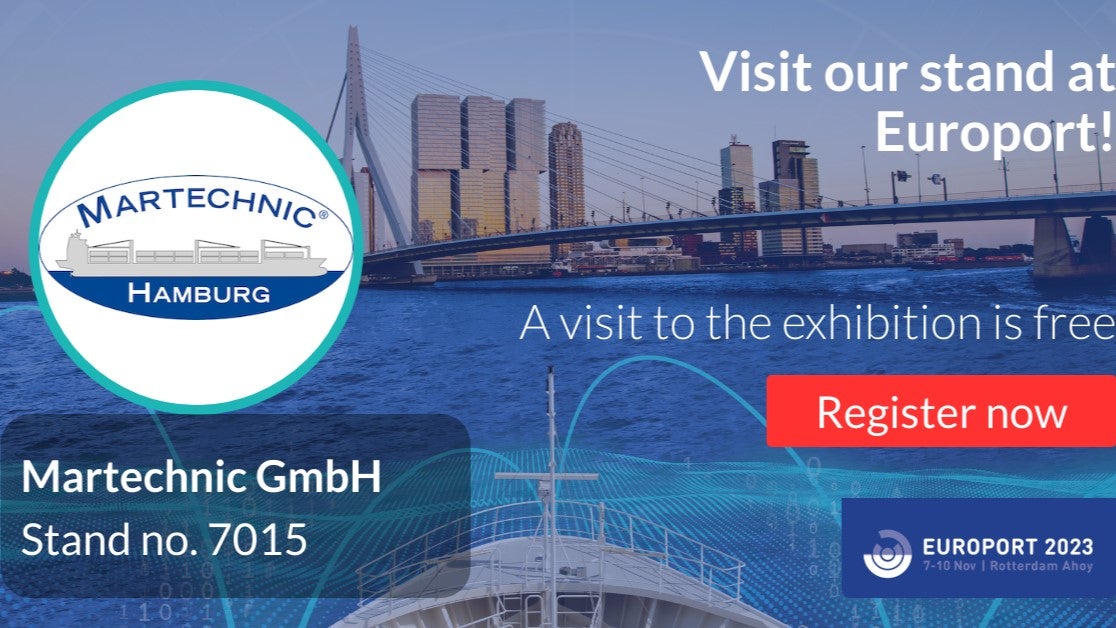
Europort is one of the largest and most important international maritime trade fairs, which provides a unique business to business (B2B) platform to maritime specialists for business cooperation, knowledge sharing, and introduction of innovative technology, with a strong focus on complex shipbuilding and high-tech ships in the challenging times of maritime transition.
Martechnic is excited to announce its participation in Europort 2023 and is inviting its customers and long-term business partners to visit its team at Hall 7, Booth 7015 within the joint exhibition area of the German Pavilion. With over 25 years of expertise in oil quality management, the company will be showcasing its high-quality technical solutions for on-site condition monitoring of fuel, lube, and hydraulic oil.
Adoption of effective, condition-based predictive maintenance practices, or in-service oil testing, with Martechnic’s precise and easy-to-use testing equipment (such as portable test devices and test kits and intelligent sensor technology) allows engineers and maintenance personnel to support the smooth running, optimal, reliable, and cost-effective operation of on-board critical machinery. Regular on-board testing and trend analysis of key oil parameters is particularly important with regard to the challenges of energy transition and the introduction of new carbon-neutral fuels, with their complex impact on lubricant performance.
Focusing on innovative technology, Martechnic will be presenting its new, patent pending test device ‘MT COOLANT CHECK’, developed for regular assessment of the engine coolant quality in the global shipping sector and beyond.
The novel measurement method of the ‘MT COOLANT CHECK’ replaces the full-scale and complex physical and/or chemical analyses of individual coolant parameters (pH, chlorides, nitrite additives) with an easy coolant diagnosis running just a single, chemical free, and environmentally friendly test. The health and condition of the engine coolant is analysed by means of the electrotechnical apparatus, with constant (corrosion resistant) and working (corrosion-prone) electrodes in a simulated engine cooling system. By applying electrical voltage, both electrodes are subjected to corrosion stress, and the performance of the engine coolant is characterised in relation to its existing level of corrosion protection with the new unit of measurement: ‘MT unit’ (‘Lagner’). As a result, precise information on further use or corrective action is provided, including clear instructions for the dosage of an anti-corrosion additive to be added so that the anti-corrosion requirements of the engine coolant are met again.