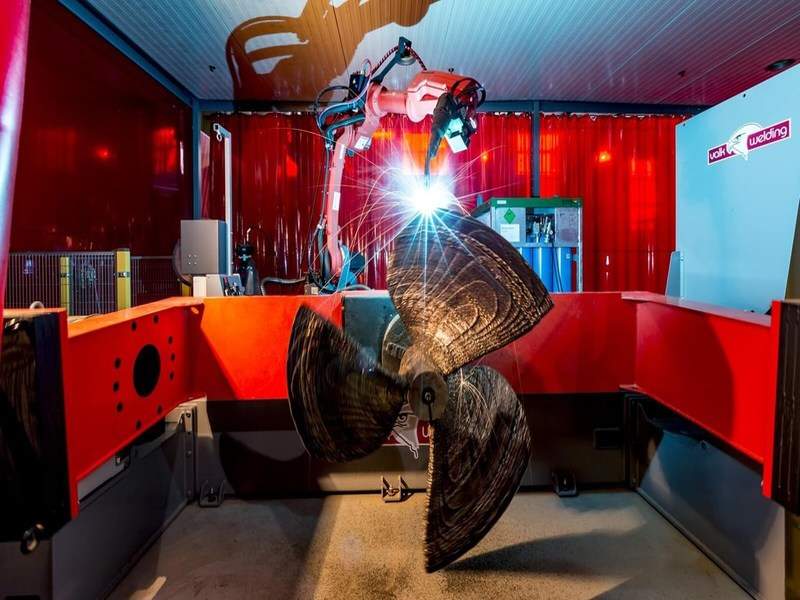
Damen Shipyard Group has unveiled its 3D-printed WAAMpeller ship propeller at its headquarters in the Netherlands following the completion of the testing process.
The propeller was developed by the company in collaboration with Rotterdam Additive Manufacturing LAB (RAMLAB), Promarin, Autodesk and Bureau Veritas.
As part of the partnership, which started seven months ago, Promarin provided the design of the triple-blade propeller.
Fabrication was conducted by the Port of Rotterdam’s RAMLAB using wire arc additive manufacturing (WAAM) techniques, while Autodesk provided software, robotics and additive manufacturing services.
RAMLAB managing director Vincent Wegener said: “Production of the second WAAMpeller was greatly improved because we had learned a lot from producing the prototype.
“This mainly concerned the hardware/software interaction because, when laying down 298 layers of nickel aluminium bronze alloy, it is important to have a tight control on all process parameters.”
How well do you really know your competitors?
Access the most comprehensive Company Profiles on the market, powered by GlobalData. Save hours of research. Gain competitive edge.
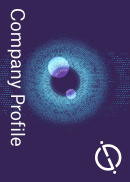
Thank you!
Your download email will arrive shortly
Not ready to buy yet? Download a free sample
We are confident about the unique quality of our Company Profiles. However, we want you to make the most beneficial decision for your business, so we offer a free sample that you can download by submitting the below form
By GlobalDataTowards the collaboration, Damen contributed research and development resources, as well as one of its Stan Tug 1606 vessels for operational testing purposes.
Meanwhile, Bureau Veritas was responsible for verification of the entire development, production and testing process.
During the testing phase, bollard pull and crash stop testing in addition to speed trials were carried out.
Damen Shipyard Group R&D project engineer Kees Custers said: “We are pleased to report that the WAAMpeller displayed the same behaviour as a conventional casted propeller in all of the tests.
“This includes the same level of performance in the crash stop scenario, which, going from full throttle ahead to full throttle reverse, is the heaviest loading that a propeller can experience.”