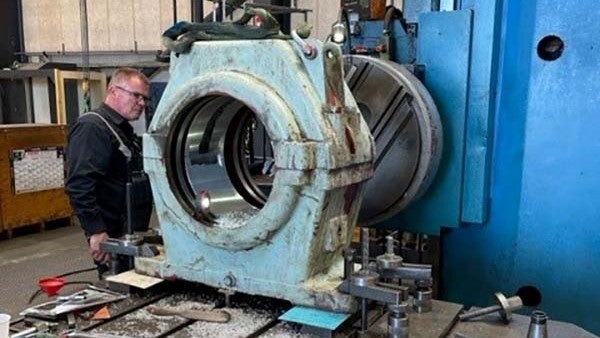
MarineShaft was called upon shortly after the damage to a chemical tanker for a repair solution and quotation.
The owner contacted the company for the repair job and it was decided that the vessel would be towed to Skagen.
Two of MarineShaft technicians got onboard whilst at anchorage off Skagen to dismantle and remove the damaged intermediate shaft bearing.
The work took place in the evening, and the following morning the vessel was towed to a lay-by berth in Skagen, where the company picked up the bearing and transported it 50km to its workshops in Hirtshals. MarineShaft used its own truck for this transport.
- In-house, the re-metaling of white metal in the split intermediate shaft bearing could begin.
- Cleaning, inspection, and measurements of the bearing shells were taken.
- Cleaning and machining of the bearing shells as preparation for soldering was carried out.
- Tinning of bearing shells as preparation for soldering with white metal was also carried out.
- The bearing shells were soldered with white metal, WM81.
- The bearing shells were matched according to the original drawing.
- Bearing control measurements were taken.
- Ultrasonic testing of the white metal’s bonding to the base material was performed by third party FORCE Technology
The owner had hired an independent surveyor, who attended the vessel, and he also visited MarineShaft’s workshop facilities in Hirtshals.
Once the in-house repair was completed, the company transported the bearing back to the vessel and the in-situ work began. This included:
- Refitting the intermediate shaft bearing.
- Load-test/jack-up testing of the intermediate shaft after installation
- Attending and supervising during the vessel’s sea trial
MarineShaft attended a successful sea trial, and the repair was fully class-approved by the Class Society ABS.
This entire job (from disassembling to installation and the final sea trial) was carried out in only eight days!
Repair and Re-casting of stern tube bearings
If you need a renewal of white metal in a stern tube bearing, MarineShaft have the capacity for centrifugal casting of up to 400kg of white metal. The white metal is melted using a purpose-built crucible furnace and the centrifugal casting is carried out with the bearing placed in the lathe.
Reconditioning or replacement
It is the company’s goal to be able to provide you with a short delivery time, no matter if you need your bearings replacing or repaired. In case the bearing housing or shells are damaged and also need to be replaced, the company has cast iron tubes suitable for this purpose in stock.
MarineShaft carries a wide variety of sizes of these tubes and have materials in stock up to Ø1000/750x2000mm.
The company also keeps a large stock of materials for manufacturing all types of components in different grades if reconditioning/repair is not an option.
Please note that MarineShaft also stocks composite-bearing materials.